Case Studies
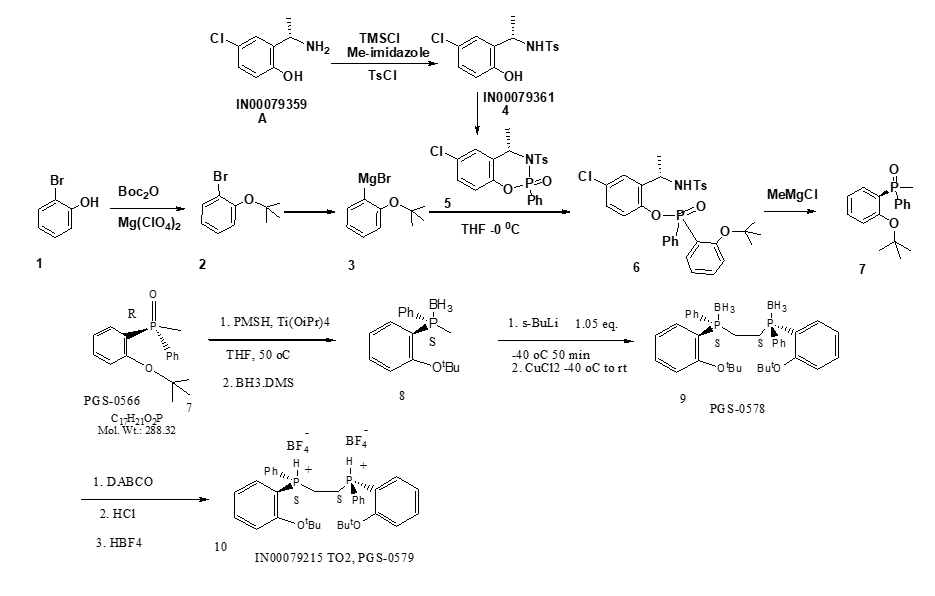
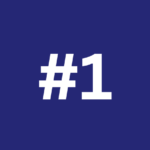
Published in JOC
- The preparation of the tosylate: the protection and de-protection wereused.
- The tBu-OPhBr formation, in the previous process, the pre-oxide ester and Grignard reagent were used for the transformation. The raw materials are of high cost and the conditions are unsafe.
- Key intermediate 6, highly flammable tBuLi was used in the old process, which was very difficult to scale-up.
- Four flash column isolation/purification were used.
- The final ligand originally was a bis-BF4 salt, but highly not stable during drying.
- Overall yield was low, 6.2% only.
- The synthesis of the tosylate, an in-situ protection with TMSCl was used, save 2 steps with high yield.
- PGS has changed this synthetic approach and used (Boc)2O as tBu transfer agent in the presence of catalytical amount of Mg(ClO4)2. The reaction was successfully scaled-up with ~79% yield.
- PGS made breakthrough change for this step and eliminated the tBuLi for this step. This major improvement has been employed in this scale-up campaign with expected results.
- The isolation and purification have been simplified for entire process. Only one flash column was used for the entire process instead of three chromatographic isolations.
- The overall yield has been significantly improved from 6.2% to 12%.
- In addition to the above achievements, another significant progress is the stability enhancement of the final product. This was a typical example of the collaboration of PGS and BI, CT during this campaign. The content of HBF4% was identified as critical controlling parameter (<26%, 2.3 eq.) for the final product stability under ambient conditions. This new finding was used as guidance for this campaign and couple of protocols were developed to reduce the residual HBF4. All batches PGS delivered from this campaign have lower levels of HBF4 (~26%) then the previous batches with 30-33% of HBF4.
- A total of >1.4 kg of the final ligand was produced and delivered with high quality and good stability, ee >99.5%, Cp >98.5%.
Case Study # 2
- 4 Coupling reactions, all need flash column for isolation/purification.
- Side-chain, tedious synthesis, difficult to make it pure.
- One coupling reaction using DMTMM reagent, the reaction easily to be stalled, requires adding more coupling reagent multiple time.
- Final API, amorphous, extremely difficult to be purified, cp only 97%.
- Total 9 + 2 = 11 steps, overall yield ~8%.
- Steps 1-2. these two reactions were performed in one-pot fashion. The work-up and isolation was eliminated.
- Step 3. After Step 2 operation, the reaction mixture was simply worked-up and Intermediate-3 stock solution in TBME was directly used for this step. After step 3, the isolated yield for 3 steps has been improved from 69% to 76% with cp >98%.
- Step 4. This is a de-Boc reaction, the 4 HCl in dioxane was used for this deprotection with high purity (>99.3%).
- Step 5. Coupling reaction using T3P as reagent, in order ensure the chemical purity (>99%)
- Step 6. After the hydrolysis with LiOH/H2O/MeOH yield 94% with cp >99%.
- Step 7. The conversion has been greatly improved from 65-75% to >98%. The additional installments of the coupling reagent becomes unnecessary. The usage of organic base has been totally eliminated. Flash column isolation/purification has been removed. The reslurry from organic solvent system is sufficient to isolate and purify the product. The isolated yield has been improved greatly from <60% to 90% with cp >94%.
- Step 8. Three different acids had been evaluated at the beginning, for the de-Boc protection reaction, HCl in dioxane, HCl in IPA and HCl in Et2O, the results were not highly satisfied in terms of the purity, color and the yield. Eventually, a new, more economic system, HCl aq. with acetone had been found to be much better than other 3 acid systems. The product was directly isolated by adding TBME and filtration as a free-flow, white solid. The crude purified by slurrying in THF provided the white solid product in >85% yield with >97% chemical purity.
Step 9. Comprehensive investigation ha been performed by PGS for this step with great success. A much better process has been developed by PGS, with yield >69% and cp >98.5% (nice white powder solid) in this step. The flash column purification has been removed. Areal recrystallization process has been developed by PGS. Previously no solvents system had been identified as an effective recrystallization solvent for this API. The chemical purify has been enriched to 99-99.4% in the first time (as a small needle crystalline solid). The overall yield has been increased from 8% to 33.8%, final API chemical purity from <97% to >99%.
- Step 1. The procedure was simplified significantly, the flash column isolation/purification were removed, the crude product was used
- Step 2. Highly tedious operations (acid-base washes have been eliminated),
simple filtration and washing with water resulted in pure product. The
NH3/MeOH solution was replaced by normal ammonium aqueous solution.
The overall yield has been nearly doubled from 35% to >70% with high
purity. This intermediate produced via the improved protocol has been used
many times for Step 7 operation. The conversion was nearly 100% for both
NXT5834-8 (99.4% by HPLC) .
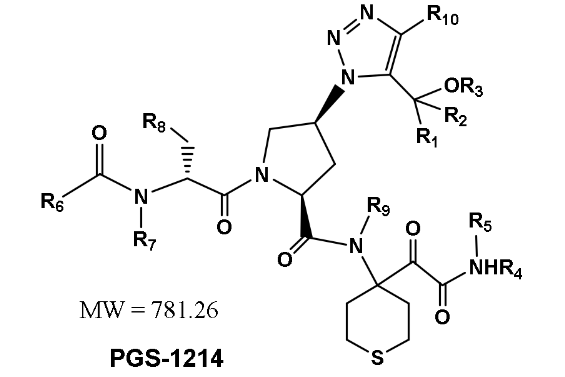
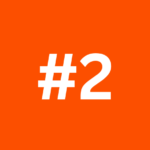
Case Study # 2
- 4 Coupling reactions, all need flash column for isolation/purification.
- Side-chain, tedious synthesis, difficult to make it pure.
- One coupling reaction using DMTMM reagent, the reaction easily to be stalled, requires adding more coupling reagent multiple time.
- Final API, amorphous, extremely difficult to be purified, cp only 97%.
- Total 9 + 2 = 11 steps, overall yield ~8%.
- Steps 1-2. these two reactions were performed in one-pot fashion. The work-up and isolation was eliminated.
- Step 3. After Step 2 operation, the reaction mixture was simply worked-up and Intermediate-3 stock solution in TBME was directly used for this step. After step 3, the isolated yield for 3 steps has been improved from 69% to 76% with cp >98%.
- Step 4. This is a de-Boc reaction, the 4 HCl in dioxane was used for this deprotection with high purity (>99.3%).
- Step 5. Coupling reaction using T3P as reagent, in order ensure the chemical purity (>99%)
- Step 6. After the hydrolysis with LiOH/H2O/MeOH yield 94% with cp >99%.
- Step 7. The conversion has been greatly improved from 65-75% to >98%. The additional installments of the coupling reagent becomes unnecessary. The usage of organic base has been totally eliminated. Flash column isolation/purification has been removed. The reslurry from organic solvent system is sufficient to isolate and purify the product. The isolated yield has been improved greatly from <60% to 90% with cp >94%.
- Step 8. Three different acids had been evaluated at the beginning, for the de-Boc protection reaction, HCl in dioxane, HCl in IPA and HCl in Et2O, the results were not highly satisfied in terms of the purity, color and the yield. Eventually, a new, more economic system, HCl aq. with acetone had been found to be much better than other 3 acid systems. The product was directly isolated by adding TBME and filtration as a free-flow, white solid. The crude purified by slurrying in THF provided the white solid product in >85% yield with >97% chemical purity.
Step 9. Comprehensive investigation ha been performed by PGS for this step with great success. A much better process has been developed by PGS, with yield >69% and cp >98.5% (nice white powder solid) in this step. The flash column purification has been removed. Areal recrystallization process has been developed by PGS. Previously no solvents system had been identified as an effective recrystallization solvent for this API. The chemical purify has been enriched to 99-99.4% in the first time (as a small needle crystalline solid). The overall yield has been increased from 8% to 33.8%, final API chemical purity from <97% to >99%.
- Step 1. The procedure was simplified significantly, the flash column isolation/purification were removed, the crude product was used
- Step 2. Highly tedious operations (acid-base washes have been eliminated),
simple filtration and washing with water resulted in pure product. The
NH3/MeOH solution was replaced by normal ammonium aqueous solution.
The overall yield has been nearly doubled from 35% to >70% with high
purity. This intermediate produced via the improved protocol has been used
many times for Step 7 operation. The conversion was nearly 100% for both
NXT5834-8 (99.4% by HPLC) .
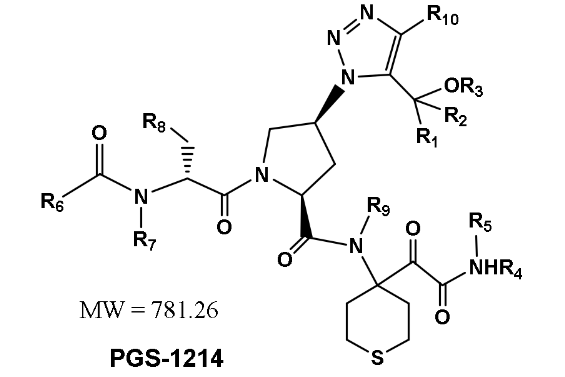
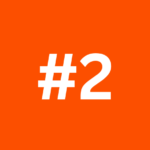
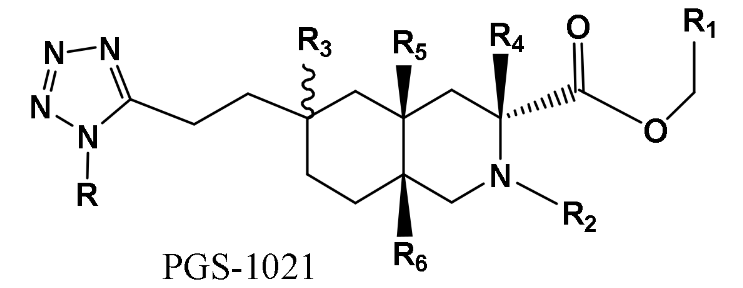
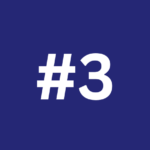
A Drug Candidate for a new indication
(Original Lilly’s Patented Compound)
- Total 12 steps with very low overall yield (<1%).
- Chiral resolution only had ~13% yield, 3 recrystallization.
- Tetrazole synthesis, lot of tar formed, difficult isolation with low yield.
- Wittig reaction, contracted to 3 companies without success.
Major Achievements & improvements by PGS:
- Steps 1-6. Overall improved from ~10% to 17.5%, cp >99%, one-single diastereomer.
- Chiral resolution improved from 13% to >42% with 99.5% ee in one-crystallization.
- Tetrazole synthesis, a 2-step process has been developed with overall 32% yield, cp >99%.
Wittig reaction, the key problem has been resolved. A scalable lab process has been developed with ~75% isolated yield. The process has been scaled-up in the kg-lab with >5 kg initial SM successfully with cp >98%, ee >99.5%.